Processes
In the digital and advanced robotics era, O.L.C.I. Engineering stands out as a pioneer in the development of innovative solutions.
From production process optimization to remote management of plants, the systems offered by O.L.C.I. Engineering have a wide range of applications.
Services and technologies offered apply to all fields of general industry, with focus on:
Machine tools tending
Tending of transfers, lathes and machining centers offers significant advantages in industry, including optimized cycle times. The robot, which is adaptable with both single and multiple gripper systems, can operate in configurations where it feeds multiple machines simultaneously. Feeding modes are multiple and customizable:
- Random feeding with vision system, ideal for maximum autonomy and versatility (Gauss certifications guarantee inertia of parts with magnets).
- Simple feeding belts, enhanced by vision systems to recognize positions.
- Automatic sorting systems with visual recognition, for both fixed and flexible placements.
- Palletized solutions for medium to long series production.
- Rotating warehouses for greater efficiency and organization.
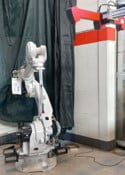
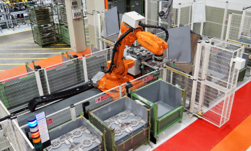
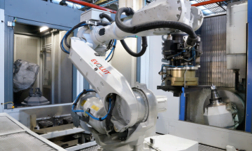
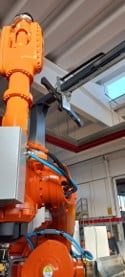
Assembly with Collaborative Robots
In the field of industrial assembly, the introduction of collaborative robots represents a revolution. These robotic cells, designed to work in synergy with humans, are characterized by a combination of precision, repeatability and safety in their movements.
Thanks to their capabilities, operators can focus on quality control tasks, ensuring excellent finished products. Collaboration between man and machine not only optimizes production processes, but also raises quality standards through a perfect balance of technical and human skills.
Special Installations
O.L.C.I. Engineering does not stop at standardized solutions. With deep expertise and a focus on innovation, the company is specialized in the design and manufacture of highly complex robotic lines.
These special systems meet specific and challenging needs, ensuring effectiveness and precision in even the most advanced and sophisticated applications:
- Assembly
- Plastic applications
- Bonding and sealing applications
- Glass applications
- Arc Welding
- Spot welding
With O.L.C.I. Engineering, robotics is elevated to new levels of excellence.
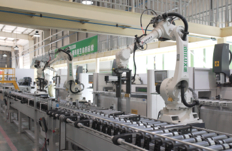
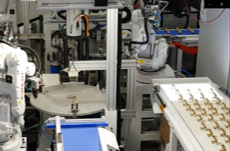
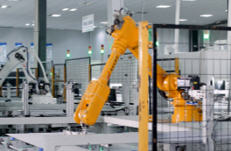
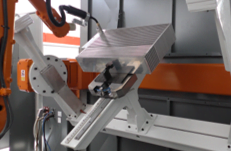

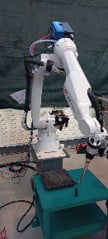
Glass Logistics and Handling
We design and implement advanced robotic systems for the glass industry, optimizing operations and ensuring precision and safety. Our solutions include:
- Depalletizing and Cutting Line Loading: we robotize the depalletizing and loading process, ensuring smooth and accurate glass handling.
- Cutting Line Unloading and Palletizing: we ensure effective post-cutting handling, allowing rapid and safe palletization of glass.
- Drilling Machines Tending: we integrate advanced robots to assist drilling machines, ensuring accuracy and repeatability.
- Management of Waterjet Cutting Machines and Scraps: robots handle glass being cut using waterjet technology and manage scrap efficiently.
- Bending Furnaces Tending: with our robotic systems, the loading and unloading of bending furnaces take place with precision, safeguarding the integrity of the material.
With our experience and expertise, we bring innovation and optimization to every stage of glass handling.
Advanced Palletizing Systems
We offer state-of-the-art palletizing solutions to ensure efficient and accurate operations.
- End-of-Line Palletizing: our cells are equipped with advanced product handling systems, packaging filmers and pallet marking devices.
- Aluminium Ingot Palletizing: designed for high production demands, these cells can handle up to 2,400 pieces per hour.
With our technology and expertise, we aim to optimize the productivity and efficiency of palletizing operations.
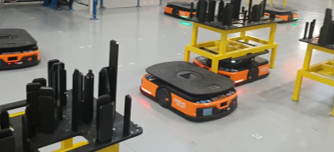
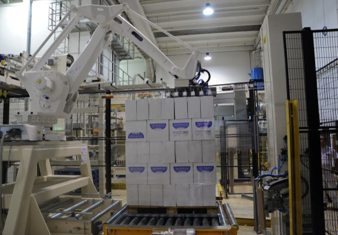
Plastic Line
Our robotic solutions are designed to handle both injection and deburring processes for plastic components. These cells can automate machine unloading by eliminating manual operations.
We also integrate cooling stations, directly operated by the robot, and offer options for palletization and packaging at the end of the line, ensuring an efficient and continuous production flow.
Welding
We design specific robot cells for Mig/Mag and Tig welding processes, supported by both standard and customized positioners according to Customer needs, ensuring accuracy and efficiency.
Foundry
O.L.C.I. Engineering provides its consolidated experience in the most different areas related to the Foundry sector, finding a prominent place in the processing of steel, aluminium, cast iron, die casting and gravity casting, as well as in multiple other solutions, such as deburring and grinding.
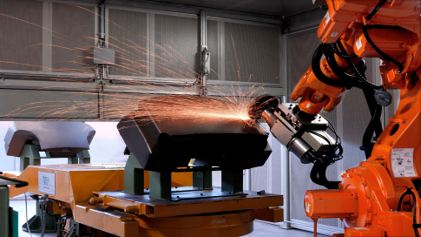
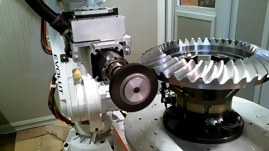
Steel
The deburring of steel castings can be divided into two different solutions:
1. With robot-manipulated castings for weights up to 200 kg and machining on stationary machines, with the possibility of different feeding systems:
- Random with the help of the vision system;
- Palletized castings with rotating warehouses;
- With reference-free belts with the help of the vision system.
The deburring units are compensated and backtracked. The pass speed is managed according to the amount of burr on the casting. Wheel wear is managed by the laser readout system.
2. With robot-manipulated spindle and jet clamped on motorized positioner for weights over 200 kg. The spindle allows quick tool changes resulting in reduced downtime. The tool deposit offers maximum flexibility and availability of different tools. Wheel wear is managed by the laser readout system.The productivity ratio of a robotic deburring cell compared to a manual one is 4 to 1.
The 3D programming software enables to set up the cell in 15 minutes instead of the usual 8 hours. This leads to a drastic reduction in the cell downtime, resulting in greater production flexibility and the possibility to process smaller minimum batches. Virtual simulation provides insight into production cycle times on a casting before it is put into production.
Turnkey plants can be built with soundproof booths equipped with extraction system.
ALUMINIUM
Aluminium cutting, deburring, grinding and satin finishing.
The cell can handle parts up to 120/150 kg in case of parts at the Robot wrist and without weight limit in case of parts placed on the table. The productivity ratio of a robotic cell compared with the operator is 4 to 1. The cell can be randomly fed with the help of the vision system, palletized with rotary warehouses, belt warehouses. Feedback and servo systems for robot gripper compensation. The cell enables quick tool changes, resulting in reduced downtime. Tool deposits, in the case of spindle manipulated by the robot, offer maximum flexibility and availability of different tools.
The 3D programming software allows to set up the cell in 15 minutes instead of the usual 8 hours. This leads to a drastic reduction in the cell downtime, resulting in greater production flexibility and the possibility to process smaller minimum batches. Thanks to the virtual simulation software, it is possible to know the production cycle times. Turnkey plants can be built with soundproof booths equipped with extraction system.
Cast iron
Cutting and deburring
The cell can handle parts up to 120/150 kg in case of parts at the Robot wrist and without weight limit in case of parts placed on the table. The productivity ratio of a robotic cell compared with the operator is 4 to 1. The cell can be randomly fed with the help of the vision system, palletized with rotary warehouses, belt warehouses. Feedback and servo systems for robot gripper compensation. The cell enables quick tool changes, resulting in reduced downtime.
The 3D programming software allows to set up the cell in 15 minutes instead of the usual 8 hours. This leads to a drastic reduction in the cell downtime, resulting in greater production flexibility and the possibility to process smaller minimum batches. Thanks to the virtual simulation software, it is possible to know the production cycle times. Turnkey plants can be built with soundproof booths equipped with extraction system.
Ramming
Core insertion with high weights, increased repeatability and accuracy of core insertion with reduction of scraps and inclusions on castings, possibility of feeding cores from pallets or on conveyors without references, thanks to position and orientation recognition by means of the O.L.C.I. Engineering vision system, while picking up.
Gravity casting
Gravity casting plants have the following features:
- Liquid metal withdrawal from crucible furnaces with metal determination by thermocouples, or from self-levelling furnaces.
- Feeding up to 4 shellers and 2 metal feeding furnaces.
- Possibility of pouring into molds with or without ladle up to 4 cavities.
- Use of the external seventh axis to handle the ladle, entirely designed by O.L.C.I. Engineering.
- Maximum metal weight: about 100 kg.
Cell type:
- With shells installed on the ground, fixed or tilting.
- With shells installed on multi-division rotary tables.
- With self-leveling basin furnace.
- With double crucible furnace.
In all cells it is possible to change the shell without interrupting the automatic robot operation cycle. The pouring cycle is programmed from the synoptic panel with simplified operator interface and dedicated keyboard, which makes the definition of points and process simple and intuitive.
Pressure die casting
Die casting plants have the following features:
- Dramatically reduced machine unloading times. The cell can be designed so as to provide a mold lubrication phase with the use of an additional robot.
- In case of anomalies, the automatic repositioning software allows the robot to be moved to an out-of-block position by means of a button.
- Customized studies can be made for deburring the part directly at the press exit, thus saving one operator passage and eliminating intermediate storage warehouses.
Others
Robotic cells for lost wax core coating
- Maximum manipulable weight of the finished cluster (mold): 200Kg
- Possibility to handle different types of materials and adhesive tanks according to the coating process.
The line supervisor manages the recognition of the cluster on the line, the number of coatings and the type of material assigned to it, as well as the drying time of the various layers. The completed cluster is automatically unloaded from the coating line for subsequent operations.
Hot molding
The robot can handle parts with temperatures up to 1100°C and can be equipped with liquid-cooled gripping systems, if necessary. Special air-conditioned cover systems protect the robot from heat radiation from the manipulated part. In case the parts being fed from the reheating furnace do not have a referenced and repetitive position, their recognition is done by cameras and vision system.
Depending on the cycle time and the temperature loss of the part, the robot can feed more than one press. Molded parts can be placed on special cooling and conforming deposits before being unloaded into the bins.
Core painting
Possibility of handling multiple cores with multigripper systems: rotating grippers that facilitate dripping after immersion into the coating product.